This article delves into the manufacturing process of super absorbent polymer (SAP).
Note: The advanced technical insights presented in this article are provided by our esteemed partners, the manufacturers of super absorbent polymer, with whom we collaborate closely. For further inquiries, detailed discussions, or questions regarding this topic, kindly complete the form to connect with our dedicated technical team.
What is the Super absorbent polymer?
A super absorbent polymer (SAP) is typically manufactured through the polymerization process of acrylic acid combined with sodium hydroxide and an initiator. This process results in the formation of poly-acrylic acid sodium salt, commonly known as sodium polyacrylate, which is the most widely produced type of SAP globally.
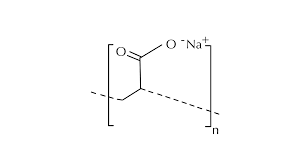
Sodium polyacrylate appears as light white crystalline particles under normal conditions. It possesses several key characteristics such as being odorless, non-toxic, and having a lightweight texture. Compared to other general-purpose resin materials, it is the lightest per unit mass and exhibits exceptional water absorption and retention properties.
In addition to sodium polyacrylate, various other materials are utilized in the production of super absorbent polymers. These include polyacrylamide copolymer, ethylene maleic anhydride copolymer, cross-linked carboxymethylcellulose, polyvinyl alcohol copolymers, cross-linked polyethylene oxide, and starch grafted copolymer of polyacrylonitrile, among others. The latter, starch grafted copolymer of polyacrylonitrile, stands out as one of the earliest forms of SAP developed.
Principle
The water absorption principle of polyacrylic resin differs significantly from that of other desiccants. It has the ability to absorb water hundreds of times its own weight, resulting in the formation of a gel. The structure of this gel is determined by the cross-linking properties of polyacrylic resin, ensuring that water cannot be squeezed out or flow beyond a specific pressure threshold.
As a result, polyacrylic acid polymers are suitable materials for synthesizing superabsorbent polymers. The water absorption capabilities of these polymers are not solely dependent on the materials used but are also influenced by the synthesis process of superabsorbent polymers.
The production process of superabsorbent resin follows several key steps
Ingredient Preparation:
Industrial-grade acrylic acid, sodium hydroxide, sodium persulfate as the initiator, and divinylbenzene as the cross-linking agent are prepared for chemical polymerization.
Distillation of Polypropylene:
Industrial-grade polypropylene undergoes distillation under reduced pressure to prevent degradation during storage and transportation. A polymerization inhibitor is added to maintain its polymerization properties. Distillation requires evacuating air from the system to avoid reaching polypropylene’s boiling point due to its low temperature resistance.
Preparation of Alkaline Solution:
Industrial-grade sodium hydroxide is dissolved in distilled water to remove impurities that could affect polypropylene’s polymerization process. The resulting filtered solution serves as the alkali solution for bulk polymerization.
Neutralization:
Distilled polypropylene is slowly added to the sodium hydroxide solution, neutralizing it. Optimal neutralization occurs at temperatures between 10-50°C, exchanging ions to produce polypropylene salt and water. Reagents are dosed carefully to ensure complete reaction and consumption.
Polymerization:
Following neutralization, sodium persulfate and divinylbenzene are added to initiate polymerization of the polypropylene salt. Polymerization occurs at ambient temperatures below 60°C for approximately 2 hours, followed by a temperature increase to 70°C for over 3 hours to form polypropylene salt gel. The gel is dried at 70-80°C to obtain solid polyacrylic acid resin, which is then crushed and ground into powder particles for industrial use.
This process outline provides a concise overview of the general production process for Natriumpolyacrylat, a commonly used superabsorbent resin.
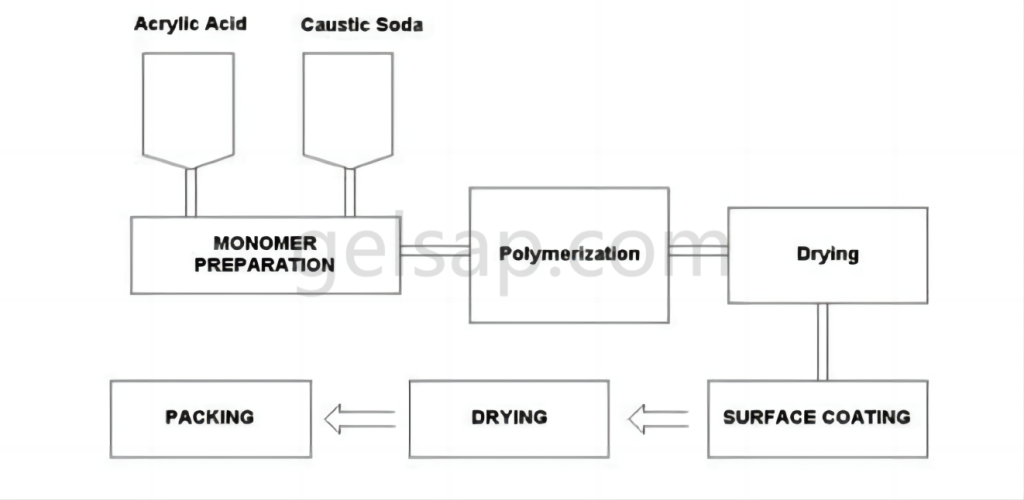
Currently, superabsorbent polymers are produced using one of four main methods: direct polymerization, gel polymerization, suspension polymerization, and solution polymerization. Each method offers distinct advantages and results in varying product qualities.
Gel polymerization
Gel polymerization using the inverse emulsion method involves converting raw polypropylene into a solvent form. This is achieved by dissolving polypropylene in a non-polar solvent, which acts as a dissolving agent, along with an oily active agent to create an oily solvent. An initiator and crosslinking agent are then added to this solution during the process.
The preparation of raw materials follows the approach of combining “polypropylene monomer + oily solvent containing initiator and crosslinking agent + lye.” The resulting solution, consisting of insoluble polyacrylate, serves as the medium for the gel polymerization process.
Method Description:
The method involves blending frozen acrylic acid, water, cross-linking agents, and UV initiator chemicals, which are then deposited onto a moving belt or into large tubs. This liquid mixture is transferred to a “reactor,” a lengthy chamber equipped with powerful UV lights that drive the polymerization and cross-linking reactions. The resulting sticky gel “logs” contain 60-70% water.
These logs are subsequently shredded or ground and transferred to various types of dryers. Additional cross-linking agents may be applied to the particle surfaces through “surface cross-linking,” enhancing the product’s ability to swell under pressure—a characteristic measured as Absorbency Under Load (AUL) or Absorbency Against Pressure (AAP). After drying, the polymer particles are screened to ensure proper particle size distribution before packaging.
The gel polymerization (GP) method is currently the most widely used technique for producing sodium polyacrylate superabsorbent polymers found in baby diapers and other disposable hygiene products.
Vorteil
One advantage of the inverse emulsion polymerization method is that it creates an emulsion by mixing the non-polar solvent containing dissolved polypropylene with the oily solvent containing the initiator and crosslinking agent. This emulsion allows polyacrylate to polymerize on the outer layer of the polypropylene solvent, forming an “oil-in-water” structure that facilitates the polymerization process of polyacrylate.
The “oil-in-water” structure effectively isolates the free performance of polyacrylate, enabling it to undergo a single polymerization function. This accelerates the reaction rate of polyacrylate, making the preparation rate of inverse emulsion polymerization five times faster than that of solution polymerization.
Furthermore, the presence of the dispersion medium not only aids in heat transfer and temperature control but also allows the polymerization of superabsorbent resin material to occur under low-temperature conditions. This method overcomes the temperature limitations typically associated with polyacrylic resin materials.
Additionally, the oil phase used in inverse emulsion polymerization can be reused multiple times. While it may not achieve the same savings as bulk polymerization, it addresses the issue of excessive waste of initiator and crosslinking agent, thereby reducing cost inefficiencies.
Suspension polymerization
Suspension polymerization shares a similar principle with Gel polymerization, particularly in utilizing a dispersant to facilitate heat transfer, temperature control variation, and accelerate the polymerization reaction rate.
However, the key difference lies in the use of phases: Suspension polymerization employs the water phase as the separate phase and the oil phase as the continuous phase. It suspends the dispersant, dissolved in polypropylene, as droplets on the surface of the oil phase, where the polymerization reaction takes place within these suspended droplets.
Like Gel polymerization, Suspension polymerization efficiently transfers heat from the reaction site due to the thermal conductivity of the dispersant. This ensures that the polymerization reaction is not constrained by temperature conditions. During polymerization, the low viscosity of alkaline substances and polypropylene minimizes the retention of unreacted impurities.
Vorteil
One advantage of Suspension polymerization over Gel polymerization is the ease of recovering its solvent through distillation, with the ability to recycle the oil phase multiple times with minimal environmental impact.
In Suspension polymerization, the water-based reactant is suspended in a hydrocarbon-based solvent. This method results in the primary polymer particle formation directly in the reactor, rather than through mechanical processes in post-reaction stages. Additionally, performance enhancements can be incorporated during or immediately after the reaction stage.
It’s worth noting that Suspension polymerization is practiced by a select few companies due to its requirement for advanced production control and product engineering during the polymerization process.
Final thoughts
In essence, superabsorbent polymers represent a dependable material known for their water absorption and retention capabilities.
The underlying principle of their preparation involves converting polypropylene into a salt form through alkali reaction, followed by a polymerization process catalyzed by an initiator and crosslinking agent, resulting in the formation of polymer substances.
In industrial settings, the preparation process is categorized into four types based on process variations. Each of these methods has its own set of advantages and drawbacks concerning preparation costs, quality, processes, and waste management. The choice of preparation process should be determined based on the specific application requirements of polyacrylic acid water-absorbing resin, considering factors like effectiveness and suitability.
For further insights or inquiries on this topic, please feel free to contact us using the form provided below.