Questo articolo approfondisce il processo di produzione del polimero superassorbente (SAP).
Nota: Gli approfondimenti tecnici avanzati presentati in questo articolo sono forniti dai nostri stimati partner, i produttori di polimeri superassorbenti, con i quali collaboriamo strettamente. Per ulteriori richieste, discussioni dettagliate o domande su questo argomento, si prega di compilare il modulo per entrare in contatto con il nostro team tecnico dedicato.
Che cos'è il polimero superassorbente?
Un polimero superassorbente (SAP) è tipicamente prodotto attraverso il processo di polimerizzazione dell'acido acrilico combinato con idrossido di sodio e un iniziatore. Questo processo porta alla formazione di un sale sodico di acido poliacrilico, comunemente noto come poliacrilato di sodio, che è il tipo di SAP più prodotto a livello globale.
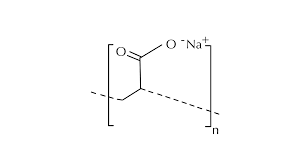
In condizioni normali, il poliacrilato di sodio si presenta come particelle cristalline di colore bianco chiaro. Possiede diverse caratteristiche fondamentali, come l'inodore, la non tossicità e la leggerezza. Rispetto ad altri materiali resinosi per uso generale, è il più leggero per unità di massa e presenta eccezionali proprietà di assorbimento e ritenzione dell'acqua.
Oltre al poliacrilato di sodio, nella produzione di polimeri superassorbenti vengono utilizzati diversi altri materiali. Tra questi, il copolimero di poliacrilammide, il copolimero di anidride etilenica maleica, la carbossimetilcellulosa reticolata, i copolimeri di alcol polivinilico, l'ossido di polietilene reticolato e il copolimero di amido innestato di poliacrilonitrile. Quest'ultimo, il copolimero di amido innestato di poliacrilonitrile, si distingue come una delle prime forme di SAP sviluppate.
Principio
Il principio di assorbimento dell'acqua della resina poliacrilica differisce in modo significativo da quello di altri essiccanti. Ha la capacità di assorbire acqua per centinaia di volte il proprio peso, dando luogo alla formazione di un gel. La struttura di questo gel è determinata dalle proprietà di reticolazione della resina poliacrilica, che garantisce che l'acqua non possa essere spremuta o fluire oltre una specifica soglia di pressione.
Di conseguenza, i polimeri di acido poliacrilico sono materiali adatti per la sintesi di polimeri superassorbenti. Le capacità di assorbimento dell'acqua di questi polimeri non dipendono solo dai materiali utilizzati, ma sono anche influenzate dal processo di sintesi dei polimeri superassorbenti.
Il processo di produzione della resina superassorbente segue diverse fasi chiave
Preparazione degli ingredienti:
Per la polimerizzazione chimica vengono preparati acido acrilico di tipo industriale, idrossido di sodio, persolfato di sodio come iniziatore e divinilbenzene come agente reticolante.
Distillazione del polipropilene:
Il polipropilene di grado industriale viene sottoposto a distillazione a pressione ridotta per evitare la degradazione durante lo stoccaggio e il trasporto. Per mantenere le proprietà di polimerizzazione viene aggiunto un inibitore di polimerizzazione. La distillazione richiede l'evacuazione dell'aria dal sistema per evitare di raggiungere il punto di ebollizione del polipropilene a causa della sua resistenza alle basse temperature.
Preparazione della soluzione alcalina:
L'idrossido di sodio di qualità industriale viene sciolto in acqua distillata per rimuovere le impurità che potrebbero influire sul processo di polimerizzazione del polipropilene. La soluzione filtrata che ne risulta serve come soluzione alcalina per la polimerizzazione in massa.
Neutralizzazione:
Il polipropilene distillato viene aggiunto lentamente alla soluzione di idrossido di sodio, neutralizzandola. La neutralizzazione ottimale avviene a temperature comprese tra 10 e 50°C, con scambio di ioni per produrre sale di polipropilene e acqua. I reagenti vengono dosati con attenzione per garantire una reazione e un consumo completi.
Polimerizzazione:
Dopo la neutralizzazione, vengono aggiunti persolfato di sodio e divinilbenzene per avviare la polimerizzazione del sale di polipropilene. La polimerizzazione avviene a temperatura ambiente inferiore a 60°C per circa 2 ore, seguita da un aumento della temperatura a 70°C per oltre 3 ore per formare un gel di sale di polipropilene. Il gel viene essiccato a 70-80°C per ottenere una resina solida di acido poliacrilico, che viene poi frantumata e macinata in particelle di polvere per uso industriale.
Questo schema di processo fornisce una panoramica concisa del processo di produzione generale di poliacrilato di sodio, una resina superassorbente comunemente utilizzata.
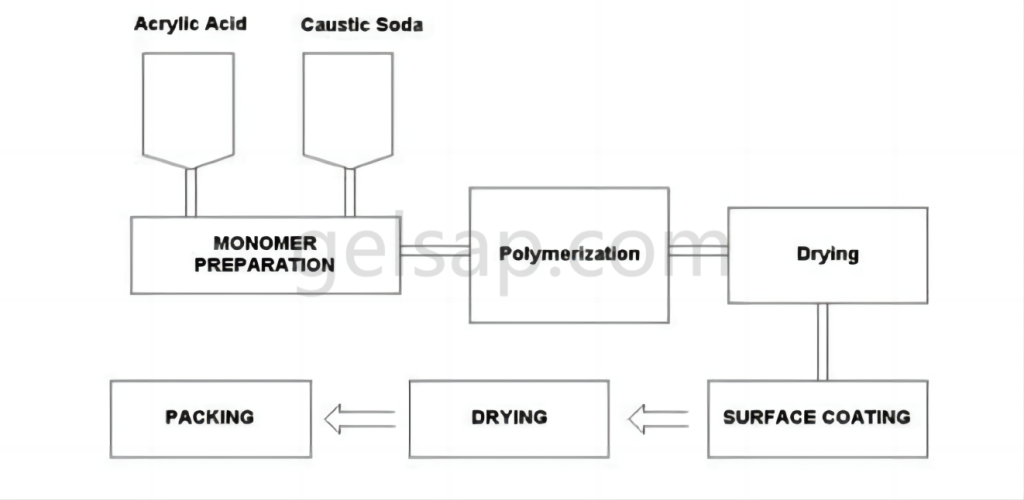
Attualmente, i polimeri superassorbenti vengono prodotti utilizzando uno dei quattro metodi principali: polimerizzazione diretta, polimerizzazione in gel, polimerizzazione in sospensione e polimerizzazione in soluzione. Ciascun metodo offre vantaggi distinti e produce prodotti di qualità diversa.
Polimerizzazione del gel
La polimerizzazione del gel con il metodo dell'emulsione inversa prevede la conversione del polipropilene grezzo in forma di solvente. Ciò si ottiene sciogliendo il polipropilene in un solvente non polare, che funge da agente dissolvente, insieme a un agente attivo oleoso per creare un solvente oleoso. A questa soluzione vengono poi aggiunti un iniziatore e un agente reticolante durante il processo.
La preparazione delle materie prime segue l'approccio della combinazione di "polipropilene monomero + solvente oleoso contenente iniziatore e agente reticolante + soda". La soluzione risultante, costituita da poliacrilato insolubile, serve come mezzo per il processo di polimerizzazione del gel.
Descrizione del metodo: il metodo
Il metodo prevede la miscelazione di acido acrilico congelato, acqua, agenti reticolanti e sostanze chimiche iniziatrici UV, che vengono poi depositate su un nastro mobile o in grandi vasche. Questa miscela liquida viene trasferita in un "reattore", una lunga camera dotata di potenti luci UV che guidano le reazioni di polimerizzazione e reticolazione. I "tronchi" di gel appiccicoso che ne risultano contengono 60-70% di acqua.
Questi tronchi vengono successivamente triturati o macinati e trasferiti in vari tipi di essiccatori. Ulteriori agenti reticolanti possono essere applicati alle superfici delle particelle attraverso la "reticolazione superficiale", migliorando la capacità del prodotto di gonfiarsi sotto pressione, caratteristica misurata come Absorbency Under Load (AUL) o Absorbency Against Pressure (AAP). Dopo l'essiccazione, le particelle di polimero vengono sottoposte a vagliatura per garantire la corretta distribuzione delle dimensioni delle particelle prima del confezionamento.
Il metodo della polimerizzazione in gel (GP) è attualmente la tecnica più utilizzata per la produzione di polimeri superassorbenti di poliacrilato di sodio che si trovano nei pannolini per bambini e in altri prodotti igienici monouso.
Vantaggio
Un vantaggio del metodo di polimerizzazione in emulsione inversa è che crea un'emulsione mescolando il solvente non polare contenente polipropilene disciolto con il solvente oleoso contenente l'iniziatore e l'agente reticolante. Questa emulsione permette al poliacrilato di polimerizzare sullo strato esterno del solvente del polipropilene, formando una struttura "olio in acqua" che facilita il processo di polimerizzazione del poliacrilato.
La struttura "olio in acqua" isola efficacemente le prestazioni libere del poliacrilato, consentendogli di subire una singola funzione di polimerizzazione. Questo accelera la velocità di reazione del poliacrilato, rendendo la velocità di preparazione della polimerizzazione in emulsione inversa cinque volte superiore a quella della polimerizzazione in soluzione.
Inoltre, la presenza del mezzo di dispersione non solo favorisce il trasferimento di calore e il controllo della temperatura, ma consente anche la polimerizzazione del materiale resinoso superassorbente in condizioni di bassa temperatura. Questo metodo supera i limiti di temperatura tipicamente associati ai materiali in resina poliacrilica.
Inoltre, la fase oleosa utilizzata nella polimerizzazione in emulsione inversa può essere riutilizzata più volte. Pur non ottenendo gli stessi risparmi della polimerizzazione bulk, questa soluzione risolve il problema dell'eccessivo spreco di iniziatore e reticolante, riducendo così le inefficienze dei costi.
Polimerizzazione in sospensione
La polimerizzazione in sospensione condivide un principio simile a quello della polimerizzazione in gel, in particolare per quanto riguarda l'utilizzo di un disperdente per facilitare il trasferimento di calore, il controllo della temperatura e l'accelerazione della velocità di reazione della polimerizzazione.
Tuttavia, la differenza fondamentale sta nell'uso delle fasi: La polimerizzazione in sospensione impiega la fase acquosa come fase separata e la fase oleosa come fase continua. Sospende il disperdente, disciolto in polipropilene, sotto forma di goccioline sulla superficie della fase oleosa, dove la reazione di polimerizzazione avviene all'interno di queste goccioline sospese.
Come la polimerizzazione in gel, la polimerizzazione in sospensione trasferisce efficacemente il calore dal sito di reazione grazie alla conduttività termica del disperdente. Ciò garantisce che la reazione di polimerizzazione non sia limitata dalle condizioni di temperatura. Durante la polimerizzazione, la bassa viscosità delle sostanze alcaline e del polipropilene riduce al minimo la ritenzione di impurità non reagite.
Vantaggio
Un vantaggio della polimerizzazione in sospensione rispetto alla polimerizzazione in gel è la facilità di recupero del solvente attraverso la distillazione, con la possibilità di riciclare più volte la fase oleosa con un impatto ambientale minimo.
Nella polimerizzazione in sospensione, il reagente a base acquosa è sospeso in un solvente a base di idrocarburi. Questo metodo porta alla formazione di particelle di polimero primario direttamente nel reattore, anziché attraverso processi meccanici nelle fasi successive alla reazione. Inoltre, i miglioramenti delle prestazioni possono essere incorporati durante o immediatamente dopo la fase di reazione.
Vale la pena di notare che la polimerizzazione in sospensione è praticata da poche aziende selezionate a causa dei requisiti di controllo avanzato della produzione e di ingegneria del prodotto durante il processo di polimerizzazione.
Riflessioni finali
In sostanza, i polimeri superassorbenti rappresentano un materiale affidabile noto per le sue capacità di assorbimento e ritenzione dell'acqua.
Il principio alla base della loro preparazione prevede la conversione del polipropilene in forma di sale attraverso una reazione alcalina, seguita da un processo di polimerizzazione catalizzato da un iniziatore e da un agente reticolante, con conseguente formazione di sostanze polimeriche.
In ambito industriale, il processo di preparazione viene classificato in quattro tipi in base alle variazioni di processo. Ciascuno di questi metodi presenta una serie di vantaggi e svantaggi per quanto riguarda i costi di preparazione, la qualità, i processi e la gestione dei rifiuti. La scelta del processo di preparazione deve essere determinata in base ai requisiti specifici dell'applicazione dell'acido poliacrilico. assorbimento dell'acqua resin, considerando fattori come l'efficacia e l'adeguatezza.
Per ulteriori approfondimenti o richieste di informazioni su questo argomento, non esitate a contattarci utilizzando il modulo sottostante.